Pages
▼
March 31, 2014
31/03/14: As the IEC celebrates its 50th anniversary, IEC Business Conference Vienna 2014 gets off to an excellent start
Over 300 leaders and decision makers from egg businesses across the world are gathered in Vienna, Austria, this week for the International Egg Commission’s Business Conference. During the next two days delegates will hear from industry experts and business leaders, as they discuss the latest trends and issues affecting the international egg industry.
Former EU Commissioner of Agriculture, Dr Franz Fischler and former ALDI Board Member and CEO, Johann Morwald will open the conference sessions on Monday morning. Dr Fischler will provide invaluable insights into EU policy and the impact on supply price and stability of feed grains, and Johann Morwald will discuss retailer expectations for the food industry.
IEC Chairman, Cesar de Anda, officially opened the conference on Sunday evening; he welcomed over 300 delegates from 30 different countries. 2014 is a significant year for the IEC, as it celebrates its 50thanniversary; to mark this milestone, the organisation will be celebrating its past while looking to the future of the industry.
Cesar de Anda told delegates: “I am delighted and proud to welcome you all to Vienna for our organisation’s first IEC Business Conference. During the next two days we will have the opportunity
to discuss the incredible strengths that our product, the egg, and our industry has to offer the world; we will also learn ways in which our businesses can become even more effective. We have a fantastic line up of speakers from across the value chain ready to share their knowledge with us on subjects ranging from retailer expectations and egg marketing, to animal influenza and the very latest research into genetics.”
In addition to the conference sessions normally associated with IEC conferences, the new IEC Business Conference will also include new focus group committee meetings, where members will discuss production & trade and economic issues in more detail.
Other speakers who will be sharing their expertise on Monday and Tuesday in Vienna include:
· Nan-Dirk Mulder from Rabobank
· Danielle Cagan from Nestlé
· Dr David Swayne from USDA/Agricultural Research Service
We will bring you daily updates from the conference, ensuring that you are kept fully up to date.
Former EU Commissioner of Agriculture, Dr Franz Fischler and former ALDI Board Member and CEO, Johann Morwald will open the conference sessions on Monday morning. Dr Fischler will provide invaluable insights into EU policy and the impact on supply price and stability of feed grains, and Johann Morwald will discuss retailer expectations for the food industry.
IEC Chairman, Cesar de Anda, officially opened the conference on Sunday evening; he welcomed over 300 delegates from 30 different countries. 2014 is a significant year for the IEC, as it celebrates its 50thanniversary; to mark this milestone, the organisation will be celebrating its past while looking to the future of the industry.
Cesar de Anda told delegates: “I am delighted and proud to welcome you all to Vienna for our organisation’s first IEC Business Conference. During the next two days we will have the opportunity

In addition to the conference sessions normally associated with IEC conferences, the new IEC Business Conference will also include new focus group committee meetings, where members will discuss production & trade and economic issues in more detail.
Other speakers who will be sharing their expertise on Monday and Tuesday in Vienna include:
· Nan-Dirk Mulder from Rabobank
· Danielle Cagan from Nestlé
· Dr David Swayne from USDA/Agricultural Research Service
We will bring you daily updates from the conference, ensuring that you are kept fully up to date.
The Global Miller
This blog is maintained by The Global Miller staff and is supported by the magazine GFMT which is published by Perendale Publishers Limited.
31/03/14: GRAPAS Speaker - Nick Wilkens
![]() |
Nick Wilkens |
Speaker: Nick Wilkins,
Director, Head of Rice Processing,
Buhler Sortex Ltd, London
Director, Head of Rice Processing,
Buhler Sortex Ltd, London
Nick, a Mechanical Engineer by training, started his career with Rolls Royce Ltd, designing aero engines. This was followed by a move to Oxford Instruments (OI) plc, a manufacturer of high-technology equipment and systems for industry, research, and healthcare. Where he was responsible for the operations of the NMR manufacturing facilities.
Nick joined Buhler Sortex Ltd in 2005 as Manufacturing Director and was responsible for the manufacture of all optical sorting, and rice processing equipment. He has been involved in the acquisition and successful integration of companies based in Brazil and China.. He has held responsibility for manufacturing facilities in the UK, India, EU & China.
For the last three years Nick has been heading Buhler’s worldwide rice processing activities.

The Global Miller
This blog is maintained by The Global Miller staff and is supported by the magazine GFMT which is published by Perendale Publishers Limited.
31/03/14: 2nd Global Milling Conference on April 23-24, 2014 in Bangalore, Karnataka, India
31 April 2014: ASSOCOM INDIA in collaboration with
United Kingdom based Perendale Publishers Limited (publishers of Grain and Feed
Milling Technology Magazine–GFMT) is organizing 2nd Version of Global Milling
Conference on April 23-24, 2014 in Bangalore, Karnataka, India. The 2nd Global Milling Conference will
be hosted in the same week in city as VIV India 2014.
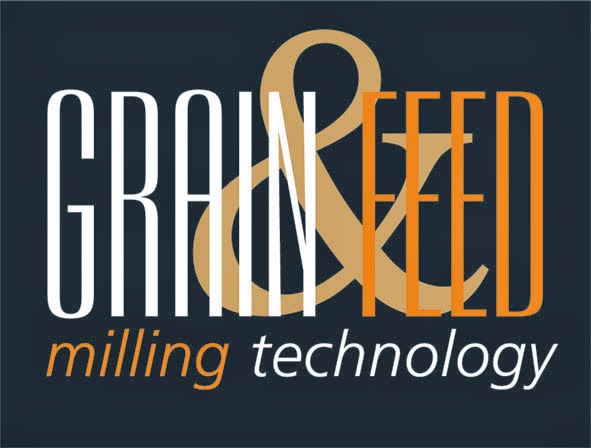
point-of-view. India with its one-billion-plus population will be a major user of milled products and a leading country in total milled grains in the decades ahead and will lead the region in technological advancements.
Dr Dinesh Bhosale, Chairman of CLFMA - the Compound
Indian Feed Manufacture’s Association - will be one of keynote presenters and
will be addressing feed technology in an industry that is booming in terms of
total feed production. He will be
joined by the Director of Indian Institute of Crop Processing Technology
(IICPT), Dr K Alagusundaram, Dr. V. Prakash, Scientist, CSIR – India, Mysore, Dr.
Ram Rajasekharan, PhD, FNA, FASc, FNASc, FNAAS Director - Central Food
Technological Research Institute Council of Scientific and Industrial Research and
Pratish Batavia, the Managing Director of PD Navakar Bio-Chem Pvt. Besides these a number of eminent
speakers shall also be joined such as Mr. Pankaj Jaiminy, Asst. Vice President
Food Certification, Testing & Inspection, TUV Sud South Asia, Dr. Y.N.
Sreerama, Senior Scientist, Department of Grain Science and Technology
CSIR-Central Food Technological Research Institute (CFTRI).
Eminent International speakers - Dr. Claus M.
Braunbeck, Sales Manger Asia of Frigor Tec, Germany; Ms. Helena Pachón, Senior
Nutrition Scientist, Flour Fortification Initiative Research Associate
Professor, Hubert Department of Global Health, Emory University; Mr. Johan den
Hartog, Managing Director, GMP+ International, The Netherlands and Mr. Roger
Gilbert, Perendale Publishers Ltd (Publisher of GFMT magazine) will also make
presentations.
Two-day conference
This year’s program covers both feed and food
subject jointly over six sessions and panel discussion which include, in
addition to the opening keynote session with its focus on UK, India and China,
will include:
Day 1
Session 1: Opening & Keynote presentation
Session 2: Food & Feed Security “Feeding 9
billion by 2050”
Session 3: Milling Developments 1 “Minimizing
energy usage in the mill”
Day 2
Session 4: Storage &
Transportation “Quality in Quality Out”
Session 5: New Technologies “What’s new
in feed and food milling?”
Processing
of cereal grains and pulses for value value-added food ingredients
Session 6: Feed & Food Heat
Treatments “Maintaining hygienic standards and the way ahead Adopting quality
control programs & regulations”
The cost to attend is Rs.10,000/-Person for Indian
delegates and US$250/person for foreign registrants. The full programme can be
seen on the following links along with registration procedures.
International registrations can be made through the
link: http://conta.cc/1dLDToE
Indian registrations can be made through the link:
http://www.assocom-india.com/gmc/
![]() |
This blog is maintained by The Global Miller staff and is supported by the magazine GFMT which is published by Perendale Publishers Limited.
31/03/14: Kendall named new President of World Farmers Organisation

Mr Kendall was elected during the final session of the WFO General Assembly in Buenos Aries, Argentina, and succeeds American Robert Carlson.
The WFO is made up of more than 50 national farmers’ organisations and agricultural co-operatives and was formed to improve the livelihoods of farmers and the viability of rural communities as well as ensuring coherence with other agriculture related activities, such as forestry, aquaculture, the environment, trade, research and education.
NFU President Meurig Raymond, who has been attending the five-day conference, said: “I would like to congratulate Peter on his election as President of the WFO. Over the past eight years he did an outstanding job for the NFU in promoting British agriculture, not just at home, but to a worldwide audience. I know that in this role he will show the same effort and enthusiasm to help develop key agricultural policies, including food security, climate change and trade.”
March 28, 2014
28/03/14: GRAPAS Speaker - Robert Zhu
![]() |
Robert Zhu |
Speaker: Robert Zhu,
Director Asian Food and Pasta Business, Buhler (Guangzhou) Food Machinery Co Ltd, China
Robert Zhu joined
Buhler in 2002, after working as the head of Technology and Production in a
flourmilling company of China, started new challenges in building up Customer
Service organizationin Buhler China.
With the experiences
gained in the China market, Robert Zhu took over the management of the grain
milling and the grain processing business. Since 2014, Robert Zhu is leading
the Buhler’s Asian food and pasta activities and is to develop the manufacturing
platform of Asian food applications.
Mr Zhu will be addressing the following topics in his presentation at the GRAPAS Conference on April 8, 2014 in the BITEC, Bangkok:
- Brief introduction of Buhler (Guangzhou) Food Machinery Co - a new joint venture acquired a local company Yaoxian Food Machinery Co Ltd is to set up a platform offering worldwide Asian food solution from China
- Main products and main market in the first stage will be strategically focus based on the existing product portfolio
- Buhler's transferred products - TPVL/TPVA continuous dough mixer manufactured in China and its application and used in China
Bentall Rowlands
28/03/14: New preconditioner: How does it increase global performance in feed extrusion processing?
The use of preconditioners
Preconditioning
systems have generally been used in feed extrusion lines (e.g. dry pet food, fish-feed)
to overcome certain
limitations that single-screw extruders have in terms of mixing efficiency,
cooking and flow capacity. They are currently used in diverse food and feed
processing applications in both single-screw and co-rotating twin-screw extruders
(TSE).
For example
in TSE production of fish-feed pellets, preconditioners are recognized by
industry specialists as being efficient because they improve productivity and
quality and allow greater flexibility in controlling process parameters.
The function of preconditioners in extrusion
The
preconditioner, located directly upstream of the extruder, is an equipment
component that makes it possible to hydrate, pre-heat and homogeneously mix
powdery raw materials with injected fluids (steam, water and potentially oil or
slurries). This operation is carried out on a continuous basis and involves
facilitating heat and mass transfer as regularly as possible between the solid,
liquid and gaseous phases. The goal is to obtain a homogeneous pre-cooked product
that is best adapted to the next stages.
The quality
of this processing depends in large part on the intensity of the mechanical
mixing, but also on the specific thermal and water diffusivity for each product,
defined by the exposure time needed for the dry material to be in contact with
the steam so that it is properly hydrated and heated. Empirically, a residence
time of about two minutes was generally used upstream in the TSE for fish-feed
flours. New fish-feed recipes –richer in vegetable proteins and with reduced
starch– and new processing throughput and quality requirements for finished
products have led to seek preconditioning times around three minutes or more.
This
increase in preconditioning processing time results in energy and humidity being
disseminated to the core of the particles, which is more efficient than simple
surface treatment, even when apparently similar temperatures are reached.
Eventually, all of the work carried out to prepare cooking and start the starch
swelling is as much energy usefully gained by the product for the following
stages of the cooking-extrusion processing.
Innovations: description of operations
Clextral has
developed a new innovative preconditioner to respond to process requirements
and increase the capacity of existing systems. In the second part of this
article, we refer to this equipment as “preconditioner+” (see Picture n°1) to describe how it operates and to
introduce the main results of experimental tests.
With the
Preconditioner +, the main function - which is to continuously ensure an
homogeneous mix of the raw materials - is carried out by two horizontal
intermeshing counter-rotating shafts, fitted with adjustable paddles (see Picture
n°2), designed to
process the product flow in an optimal way. According to the specific throughput
and the physical and chemical properties of each material being processed, it
defines a distribution and filling ratio in the mixing unit, directly linked
with the residence time required in the end.
The key
innovation of the Preconditioner +, always aiming to improve heat and mass
transfer to the product, is to integrate an Advanced Filling Control device (AFC)
which interacts directly on the material inside the mixing chamber and which
enables the filling ratio to be adjusted. This AFC system uses a special
designed screw inside the tank, and modifies favorably the flow by enabling a
partial and controlled recycling of the material being processed, from the
outlet to the entry point, thus intensifying the specific preconditioning
functions.
In
addition, the AFC system does not just increase the filling ratio, but also
generates better product distribution, in particular in the first third of the
mixing chamber which is the preferential zone for steam injection. To achieve
this, the different adjustable water and steam injection ports have been
optimally positioned –axially and angularly– to enhance absorption and product
exposure time during the mixing stage.
Experimental measurements on the Preconditioner +
Extensive
experimental trials on processing effects have been carried out on the
preconditioner+ to assess the improvements generated by its AFC system on the
twin-screw extrusion process. In this case, a standard fish-feed recipe (basic salmon feed) was used,
without necessarily seeking optimal performance to begin with, but to set an
objective benchmark compared to traditional preconditioning systems.
The first
significant observation was a lowering of the SME (Specific Mechanical Energy)
required in the extruder
–an average of 3% with equal extrusion parameters– mainly due to the increase
of preconditioning time, and largely compensating the additional consumption of
the preconditioner. As mentioned previously, this efficient pre-cooking also
enables a reduction of the shearing and the torque used in the extruder, which
also is beneficial in reducing the wear of the screws and barrels.
By focusing
exclusively on the preconditioner, the experiment also demonstrated that the
new filling ratio (up to 75%) achieved by using the AFC, made it possible to
increase residence time by 60% for an equivalent fish-feed flow and therefore to go beyond the
average of three minutes sought. At the same time, the combination
filling/steam distribution made it possible to increase the product temperature
by 3-4°C at the outlet of the preconditioner, using comparable steam injection.
It is even possible to achieve product temperature of over 96°C with optimized
steam injection, while limiting energy loss thanks to the new design. Following
the improvements on the pre-cooking stage, we were able to measure a
significant increase of the gelatinization of starches before their insertion
into the extruder.
Finally, on
the finished product after extrusion, granulation and drying, these upstream
modifications resulted in increased hardness of the pellets of at least 10 to 15%,
an essential quality criterion required for their use in fish rearing farms.
Functional advantages of the Preconditioner + in industrial applications
Beyond the
process benefits on product quality, it is important to stress that this
equipment has also been designed to facilitate industrial applications, in
particular due to the increased flexibility provided by the AFC. This variable-speed
device makes it possible to adjust the residence time as required and thus
adapt the equipment to different types of recipes, thus responding to the need
to have multi-product extrusion lines. Moreover, this convenient design allows
the system to start up when fully charged, even after prolonged down time with
a full tank, thanks to the new kinematic feature.
In terms of
hygiene or food safety, the design of the preconditioner+ limits to a strict
minimum the retention areas and thus greatly facilitates cleaning. This feature
is further enhanced by an integrated “quick recipe change-over” function
through the reversible AFC system, used here as a conveying screw that enables
the entire tank to be emptied. These improvements in equipment cleaning
capabilities and hygienic design are non-negligible advantages, in particular
in food processing applications.
Eventually,
the intensification of the preconditioner provides improvement in the overall
process, energy savings and enhanced quality of finished products, as well as
greater flexibility and better control of operating parameters, whatever the
recipe.
Furthermore,
the preconditioner can be easily adapted to single-screw or twin-screw
extruders in various food processing applications that require a mix or the
pre-cooking of raw materials, such as those used for making pet foods, corn
flakes, pre-gelled flours or starches, pellets, etc.